This is the second installment in our three part series about the nuts and bolts of how to achieve greater supply chain agility. You can find part one here. While 2022 was full of experts shouting from the rafters about how agility helps save money and increase efficiency, almost no one was offering specific steps to actually achieving that agility.
In our webinar, From Buzzword to Reality: 7 Ways to Actually Increase Supply Chain Agility, my project44 colleague, solution engineer Elizabeth Labuzienski, and I presented concrete examples of proven and practical ways our supply chain visibility platform – Movement – helps organizations reduce delays, cut costs, and improve overall efficiency. We’ll show you how in this post.
In the first part of this series, we covered three strategies and tactics related to planning. In this installment, we look at two key strategies for improving in-transit efficiency. And in the final installment, we round out our collection of 7 key ways supply chain professionals can move beyond buzzwords with two critical efficiency strategies that focus on process automation.
1. Reduce fees and dwell time with detention and demurrage analytics
The Challenge:
It’s no secret that keeping track of and managing the real-time whereabouts of each order can quickly become a time consuming and even overwhelming task, especially if you’re just one person in charge of managing hundreds and hundreds of orders.
There is often very little visibility into the most pertinent details, and getting any information at all usually requires the use of complicated manual processes like self-made reports, complex spreadsheets, and other jerry-rigged workarounds. And even when you’re able to cobble together a semi-effective solution, it rarely delivers even marginally up-to-date information (never mind real-time status) and takes a lot of time and effort to manage.
The Risk Factors:
When it becomes too difficult or too time consuming to keep up with accurately tracking each container’s location and status, a lot of companies just take detention and demurrage fees on the chin. They chalk it up to being a cost of doing business. The problem is, those fees can add up quickly – sometimes to the tune of hundreds of thousands or even millions of dollars annually. At the end of the day, that expense can have a very real, negative impact on your overall bottom line.
How Movement from project44 Can Help:
To effectively and efficiently manage container tracking, you not only need highly accurate ETAs, you also need a singular dashboard that tracks all your containers – not just their locations, but also specifics about where they are in terms of free days before they incur a penalty. This is the level of detail you need in order to successfully mitigate high detention and demurrage fees.

The Movement platform shows you exactly which containers are in each port of discharge, how long they’ve been there, and whether they are at risk for demurrage fees – all in one easy-to-access and -read dashboard.
This information allows you to proactively manage your detention and demurrage within your network, which in turn allows you to adjust routes to meet appointment schedules based on project44’s machine learning-derived ETAs. The combination of these two key capabilities puts you in a position to always stay one step ahead of any potential issues.
Benefits:
Achieve an average 10 – 30% reduction in detention and demurrage fees.
See fewer and shorter delays and dwell times.
Manage exceptions quickly and efficiently because everything is accessible in one easy-to-use dashboard.
Real-world Use Case – Saving Hours of Time Each Week:
One customer who had previously been managing hundreds of containers using her own, self-designed spreadsheets and manual processes estimates that she will save hours and hours each week by switching to the Movement Platform. In addition, because her old system was far from foolproof, she improved overall accuracy of which containers were incurring fees and saved additional time by being able to quickly isolate and focus on exceptions.
2. Eliminate excess spending and increase cash on hand with predictive ETAs
The Challenge:
As is the case for so many parts of successful supply chain management, making the right transportation mode decisions requires that you have great confidence in your ETAs and fully trust your lead time information for each mode. Without this information, you’re stuck making your best guess, or just forging ahead with the status quo and hoping everything turns out in your favor. Today’s professionals need more confidence and more intelligence to overcome a supply chain experiencing more disruptions than ever.
The Risk Factors:
The risks are two-fold. First is choosing the wrong delivery mode, which can result in stock-outs that leave customers frustrated and unhappy. Second is overcoming lack of confidence in lead times by expediting freight, most often via air, which is the most expensive mode and can eat into profit margins and cash on hand. So, you can either have unhappy customers without any additional fees, or have happy customers with lower profits. Neither scenario is particularly appealing.
How Movement from project44 Can Help:
The solution is simple, but not easy: make sure your team has access to accurate ETAs for each mode, and a predictive end-to-end ETA that you can really trust. This is the only thing that will enable you to make delivery mode decisions with confidence and determine when expedites are truly required by mapping the order arrival time you can trust with safety stock levels.
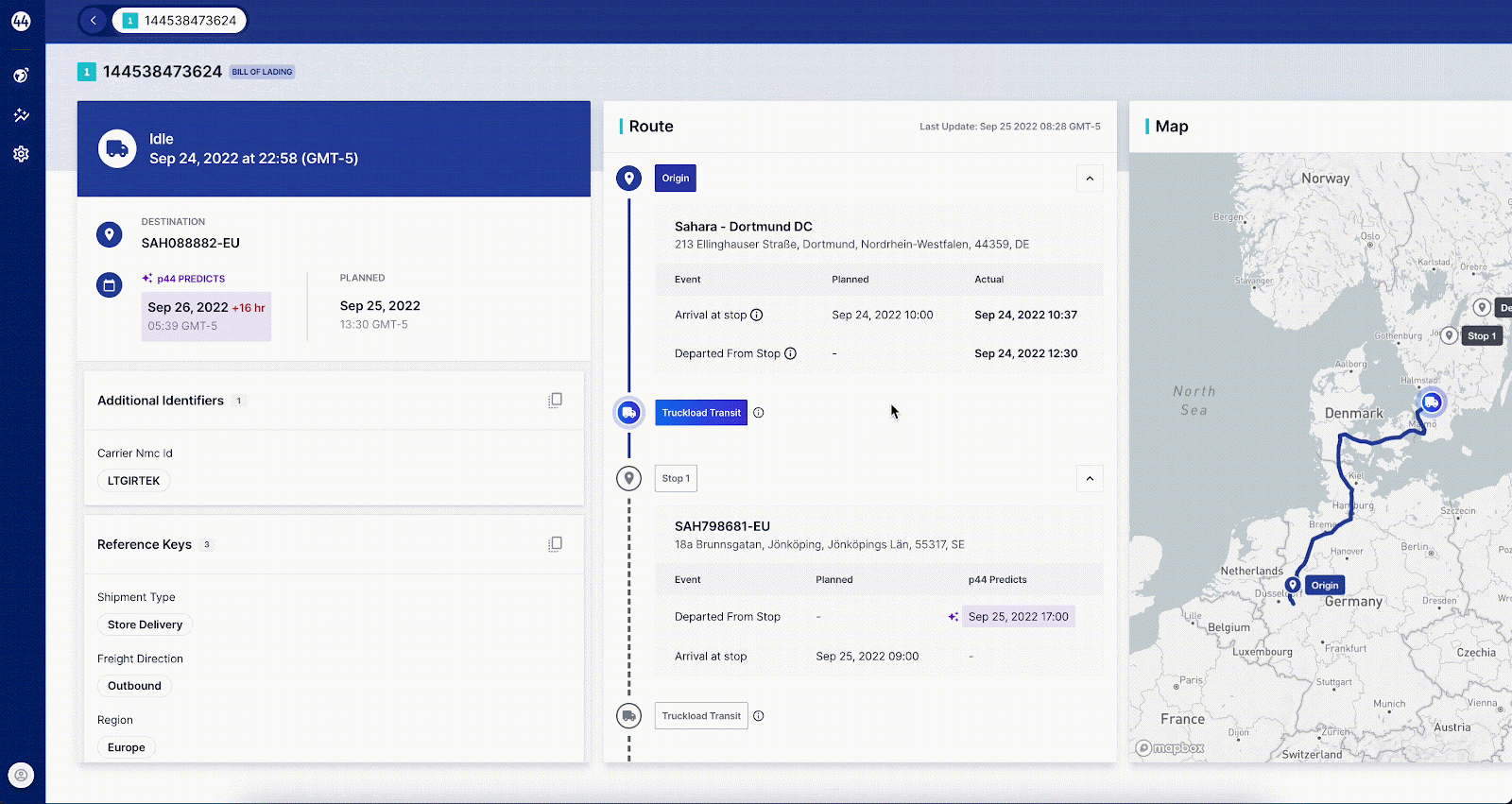
Benefits:
Save time and money by letting the Movement platform put all the relevant information at your fingertips so you can avoid having to piece together individual data points and do time-consuming independent research.
Make decisions further up the supply chain, and eliminate the buffer time to keep goods moving more freely.
Source capacity based on real-time constraints, which allows you to reduce expedite fees and the chance of choosing the wrong delivery mode.
Real-world Use Case – Comparing Transit Times to Make Strategic Decisions:
One customer used the Movement Platform to improve their mode decision making for shipping from China to Melbourne. Because the dashboard allowed them to easily see a wealth of highly relevant information about the transit times by lane (not only the but also the variability), they were able to quickly and accurately identify the best lane for their transshipment. In one specific case, they were considering three different options for transshipping in Shanghai, Ningbo, and Hong Kong respectively. Using Movement, they were able to easily compare the transit times, determine the quickest option, and then make a strategic decision based on whether they had enough lead time to go with a lower-cost option, or if they needed to pay a bit of a premium to save twelve days. It was a win-win either way because they had the information they needed to make a really well-informed choice with a known outcome.
Supply Chain Success: The Right Information at the Right Time – All in One Place
When it comes to supply chain success, what you don’t know definitely can hurt you. Having access to detailed, real-time information in a centralized location is absolutely critical to improving your efficiency, agility, and – by extension – your profitability. You need trustworthy data at your fingertips so you can get ahead of any potential issues, proactively manage all your shipments, and keep both your customers and your bosses happy.
If you’d like to hear more about these two in transit-related strategies as well as the five additional strategies we talk about in the other two installments of this series, you can tune in to view the on-demand webinar replay.